How Can You Improve Diagnostic Efficiency? Just Ask
I was talking with the owner of a fairly successful shop in Boston the other day. He told me that, although his technicians’ productivity is above average, they still seem to have problems making flat rate on diagnostics. The shop has all the latest test equipment, plenty of diagnostic and repair information and well-trained techs. He asked, “What the heck are we missing?”
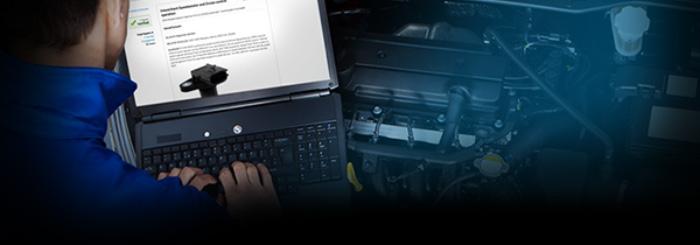
“Go back to basic diagnostic techniques,” I replied. And here’s what I meant. While most technicians possess the gift of deductive reasoning and state-of-the-art test equipment, they sometimes forget to follow some basic diagnostic techniques. No matter the type of vehicle or how complicated the problem, basic diagnostics begin with asking the right questions. Let’s explore how asking questions throughout the diagnostic process can save time and improve results.
It Starts on the Service Drive
Symptom descriptions included on the repair order must be comprehensive and accurate. The more detailed the symptom description is, the less work the technician will need to do. A complete symptom description also minimizes the risk of “fixing the wrong problem” and helps determine where to start the diagnosis. What is the key component in communicating the customer’s concern to the technician? The service advisor has to ask the right questions.
A checklist-style form that helps ask vehicle owners the right questions regarding their vehicle’s problems is a valuable tool. Where can you get these types of forms? You could create your own or you can use system-specific inspection forms and checklists developed by the Automotive Maintenance and Repair Association (AMRA) for their Motorist Assurance Program (MAP). Included in ALLDATA’s repair products under Shop Operations, these system-specific forms really help the service advisor get all the facts the technician needs to perform a quick and accurate diagnosis.
Ask the Customer for Help
You can’t fix what you can’t duplicate! Be sure to duplicate the exact conditions that cause the symptom(s) to occur. In other words, if the engine misfires only between 40-50 mph, don’t drive at 65-70 mph. This seems like simple advice but this detail is often overlooked.
What do you do when the customer’s concern can’t be duplicated? I’ve found it very beneficial to ask the owner come down and test drive the vehicle with you. Let them drive. A customer’s driving habits may differ from yours. Often the symptom can’t be duplicated. Other times, the way the owner drives the vehicle will reproduce the problem more consistently. In either case, the technician benefits. If the problem doesn’t occur, the owner believes you really tried. If it does, you know exactly how to drive the vehicle to duplicate the problem. Now it’s time to call on your scan tool for help. Plug it in, set it to record the PID information and go on a test drive.
Keep a Positive Attitude
In troubleshooting, as with any other challenge, a positive attitude will lead to success. You can solve the problem. Don’t panic, don’t get frustrated—be patient. The best way to achieve and maintain a positive attitude is to remember that it’s a mathematical certainty that you will solve any reproducible problem. Above all, remember that your troubleshooting power comes from your troubleshooting process. A well-developed process will be one you can trust time after time. But what do you do when you get stuck? Ask yourself, “Am I too close to the problem?” or “Maybe I need a second opinion?”
Working as a Team
Most shops usually charge an hour for diagnostic time. If you have spent time looking at technical service bulletins, followed a diagnostic flow chart and exhausted the limits of your past experience, you may have consumed more than an hour—with no resolution.
Before you reach the end of the hour, ask for help. Check with other techs in your shop, post the symptoms and the tests you’ve done on an automotive forum, or subscribe to a diagnostic help line. Often times, these resources have had different experiences and training. Teamwork and information sharing can be very beneficial in a shop environment. This not only results in getting the vehicle back to the customer more quickly, it also fosters positive working relationships among technicians.
Whatever the future holds for the automotive industry and no matter how technical vehicles become, invariably there will be “break downs.” And although vehicles have become more complex, the basic rules of diagnosis haven’t changed. What has changed is the quantity of diagnostic information, the method of its delivery and the technological capabilities of automotive test equipment. As technicians, our job is to repair vehicles quickly and completely. To do that, sometimes we just have to ask the right questions.
Want to see how ALLDATA can improve shop efficiency? Check out our suite of products, each designed to contribute to both shop efficiency and productivity.
If you would like to read more articles like this one please subscribe to ALLDATA News.
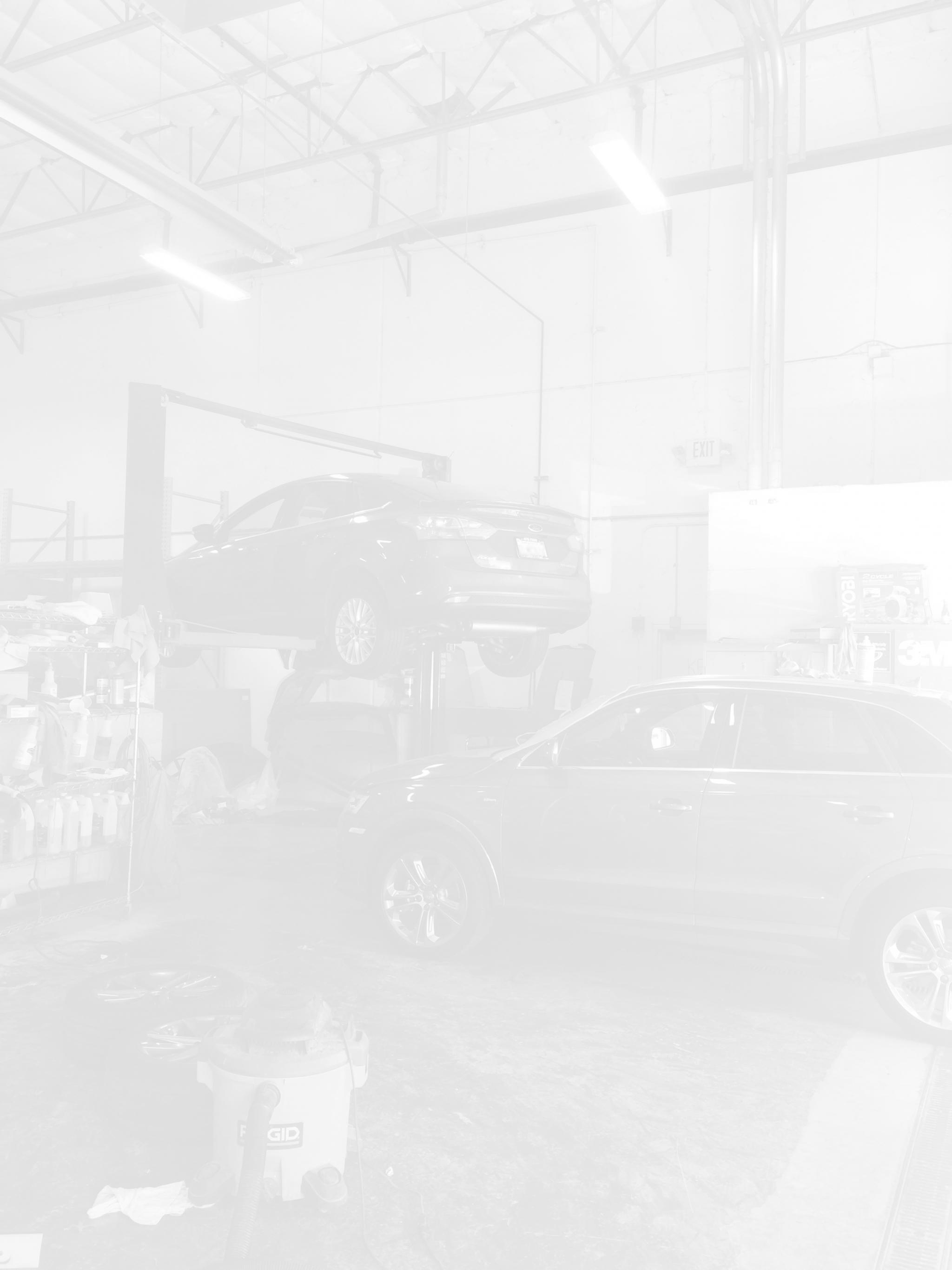