When it comes tor finding qualified techs, it’s all pain, no gain for shop owners
We know it’s a significant problem. So this past January, we surveyed shop owners, service writers, and technicians and across the country to get their take on the technician shortage in the automotive repair industry.
What did they say is the primary cause? And what should the industry do about it?
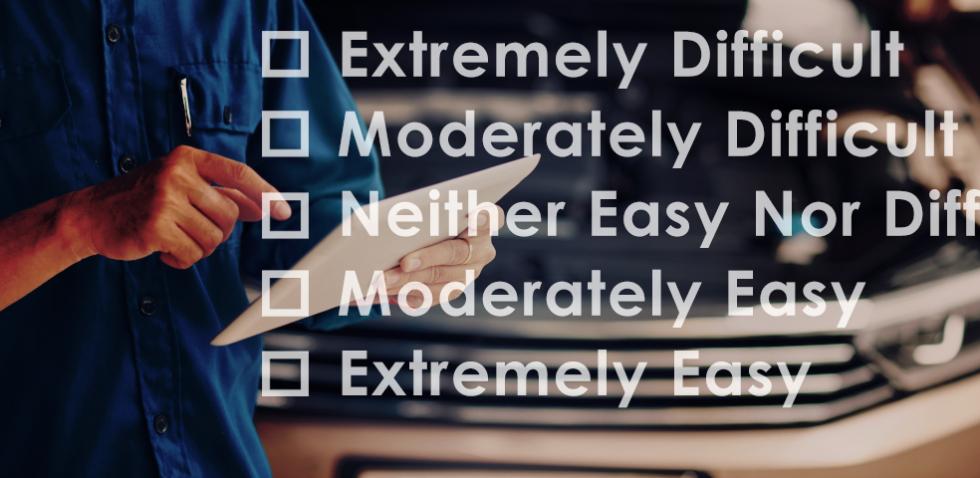
Question: How difficult is it to find qualified techs?
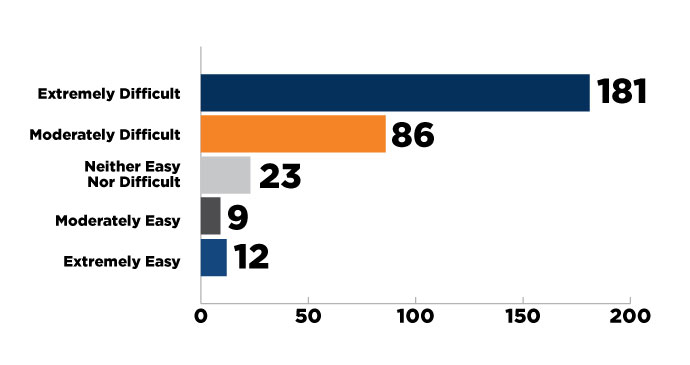
84% say it is “Extremely difficult or moderately difficult.”
Some cite declining interest in the field. Joe W. of Minnesota is just looking for technicians with “… a humble attitude and a desire to learn.”
Another big “No” – 54% of you say that private/public automotive training schools in your area aren’t providing the education technicians need.
Question: How long do you keep your techs? | ![]() |
Question: Are the training schools in your area providing the education techs need?
59% say “No.” Part of the problem cited is lack of access to local technical schools or training institutions. Part of it is the curriculum doesn’t address today’s shop needs.
Many of you want to see automotive repair back in the high schools, like Bill M. of Ontario, Canada, who says, “Provide more tech-oriented programs in our high school system.”
This opinion is echoed by many, including Linda of New York, who notes that “Schools for auto industry are not in abundance like community colleges or private colleges. If there were more schools to choose from, maybe it would be more appealing for the newcomer to adventure into the mechanic field.”
Question: Are techs being trained on data acquisition products?
72% say “Yes” – techs are being trained on data acquisition products like ALLDATA. We think this is great news! As vehicles become more and more complex, familiarity with OEM data acquisition products is essential across the general repair and collision industries.
In a recent article, Repairer Driven News also reported on shops using OEM repair information, based on Who Pays for What?, a series of annual surveys from Mike Anderson’s Collision Advice and CRASH Network. As such, the results reflect mostly collision shops’ responses.
“ | “Who Pays for What?” data last year revealed 60.5 percent of 488 surveyed shops reported researching OEM repair procedures at the time of the estimate either all or “Most of the time,” a big leap from the 48.8 percent of the 494 respondents in 2017.
However, only 24.8 percentage points of that 60.5 percent shops were researching procedures every time. The majority, 35.7 percentage points, still fell short of what experts advise should be done with their “most of the time” answer. Excerpted with permission from Repairer Driven News. | ” |
The same article notes, “2018 also saw OEM and some third-party repair procedure aggregator websites grow usage. ALLDATA remained the most popular source of repair procedure information, at 72.4 percent of 489 respondents using it, according to the “Who Pays?” data. That’s up from 68.2 percent in 2017.”
Question: What skills would you like to see in incoming technicians?
“Electrical, electrical, and more electrical,” says Sean R. of Michigan, along with many, many others.
That’s about the gist of it. Overwhelmingly, shops want technicians with electronics knowledge and experience. Diagnostics followed close behind.
“Diagnostic skills in all categories, says Robert G. of Kentucky, “Focus on how to diagnose and how to use those tools for diagnosis. I believe only a small percentage of technicians can use a scan tool, DVOM or scope and really understand the tool and what tests are available.”
And quite a few of you called out customer service.
“Customer service is our number 1 priority, not rushing jobs and performing their jobs honestly,” says Tera from Oregon.
“Electrical testing is a main need, but customer service is VITAL,” says Dean L. of Minnesota.
Question: Does your shop support ASE certification?
One way that shop owners encourage their technicians’ training is by recognizing the achievement of ASE certification.
70% of you report covering all of part of the costs associated with ASE certification and ongoing training. Many of you reward the technician with a bonus or wage increase once the test is successfully passed. And at least one of you is making training mandatory every 90 days.
The other 30% reports issues with ASE or a preference for I-CAR or other certification, with other reasons as listed below.
YES – 70% offer some or all …
- Pay for the test when passed
- Provide bonus or raise after passing
- Require certification and ongoing training
NO – 30% reasons why not …
- I-CAR (or other) certification instead
- Think consumers don’t care about ASE certification
- ASE needs better quality tests
- Techs aren’t driven for self-betterment
- Require something more specialized
- Certified techs don’t mean quality techs
- ASE doesn’t offer training
- Cost
Question: How can the industry improve technician education?
Responses to this question were as varied as they were passionate. Like this one from Dennis W. of Colorado: “There needs to be a society reset of attitudes towards young people entering the auto repair industry. Becoming an auto tech does not mean you draw the short straw.”
One of the most popular responses (see below) called for adding more opportunities for technician training, at both the school level and in the shops.
Most popular responses
- Invest in more quality education/training
- Lower costs of training/certifications
- Start programs younger
- Include more hands-on training/apprentice programs
- Better industry support
- Continuous training
- Require licensing
Question: How should the industry bring more interest to the field?
Finally, respondents offered their take on how to fix the shortage. It boils down to raising pay, providing training, and changing mindsets. Pretty tall order.
“ We keep employees a long time by paying well, giving great benefits and training, and don’t micro manage.””
Charles B. from Pennsylvania
“In order to draw the best and brightest people into the industry, we must offer compensation that is competitive with other industries,” says Ronnie B. of Tennessee.
This strategy seems to be working for Charles B. of Pennsylvania. “We keep employees a long time by paying well, giving great benefits and training, and don’t micro manage.”
Chrystal C. of Indiana suggests, “Develop a nationwide certification standard required to be a mechanic, like licensing a plumber or electrician.”
We feel your pain
Our survey confirmed what we already know – the technician shortage is putting shops in a world of pain. Lack of educational opportunities, negative public perception, and low pay all present significant challenges for attracting and keeping qualified auto repair technicians.
Or as Gene M. of California puts it, “There is no technician shortage, it is a perception and poor image issue. Pay a great wage with great benefits. Problem solved.”
We appreciate everyone who participated in the survey and will continue to explore this topic in future issues of ALLDATA News. See the survey methodology below
Survey methodology
We distributed the survey to shop owners, service writers, and technicians.
Who weighted in – shop demographics
Shop role | > | Primarily shop owners, followed closely by shop managers. |
# of Bays | > | From one bay to more than 11, but most shops have four to five. |
# of Techs | > | The majority of survey responders employ two or three techs. |
How Long? | > | 43% have employed their techs for eight-plus years. |
Location | > | From coast-to-coast and as far north as Fairbanks, Alaska. |
Want to see how ALLDATA can improve shop efficiency? Check out our suite of products, each designed to contribute to both shop efficiency and productivity.
If you would like to read more articles like this one please subscribe to ALLDATA News.
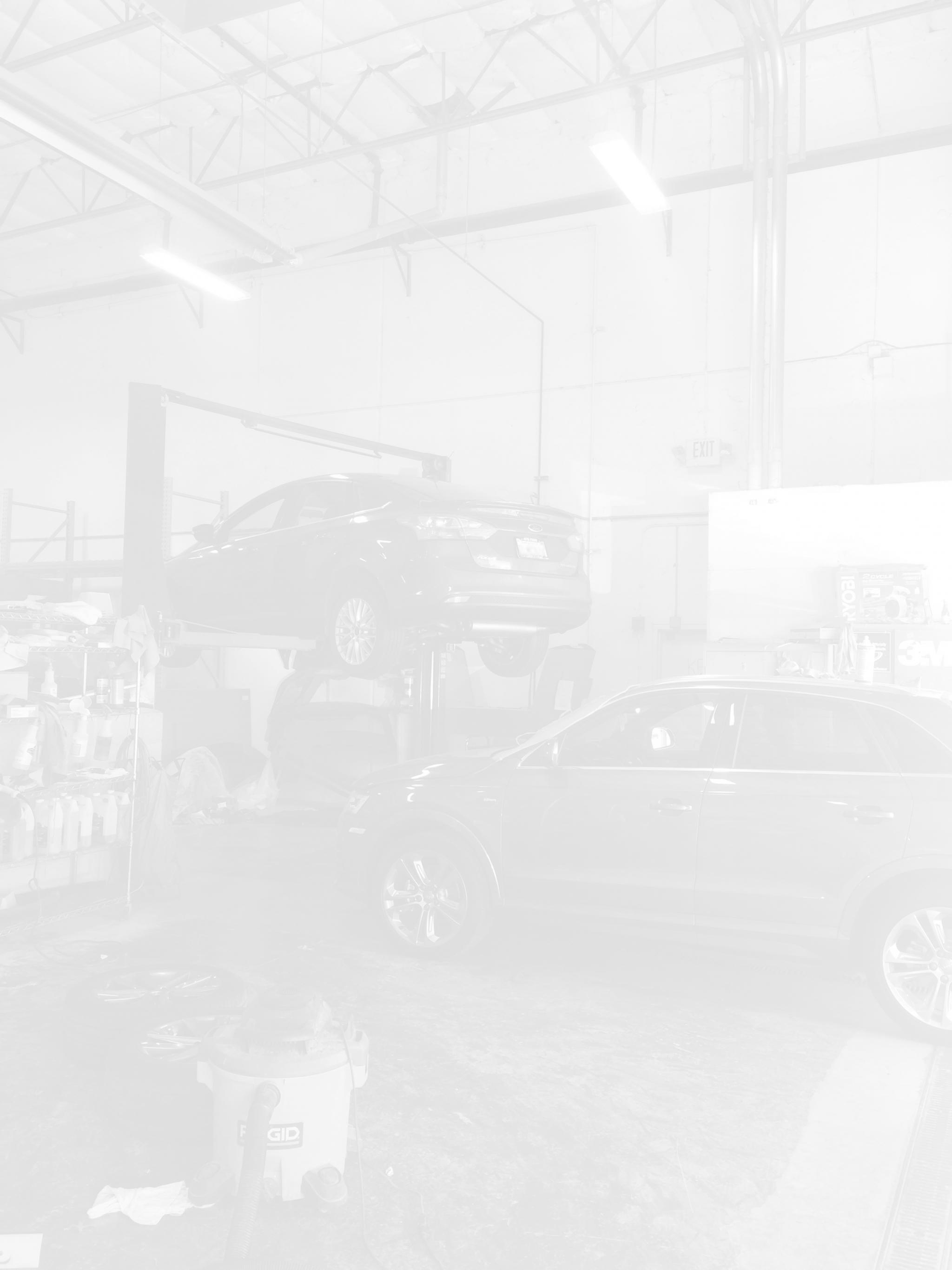